Inconel 718 nickel-based alloy, known for its exceptional mechanical properties and corrosion resistance, has found widespread applications in various extreme environments. This article will explore in detail the elemental content, application areas, and advantages of 718 nickel-based alloy.
Elemental Content of 718 Nickel-Based Alloy
718 nickel-based alloy is an alloy containing a large amount of nickel, along with elements like chromium, iron, copper, molybdenum, aluminum, and titanium. Its main chemical composition includes:
Nickel (Ni): 50.0-55.0%
Chromium (Cr): 17.0-21.0%
Iron (Fe): Balance
Boron (B): 0.006%
Silicon (Si): 0.35%
Molybdenum (Mo): 2.8-3.3%
Sulfur (S): 0.015%
Copper (Cu): 0.3%
Aluminum (Al): 0.2-0.8%
Titanium (Ti): 0.65-1.15%
The high nickel content gives 718 nickel-based alloy excellent corrosion resistance and high-temperature stability. Chromium and iron contribute to its good mechanical properties and wear resistance, while the addition of copper, molybdenum, aluminum, and titanium further optimizes the alloy’s performance.
Mechanical Properties of 718 Nickel-Based Alloy
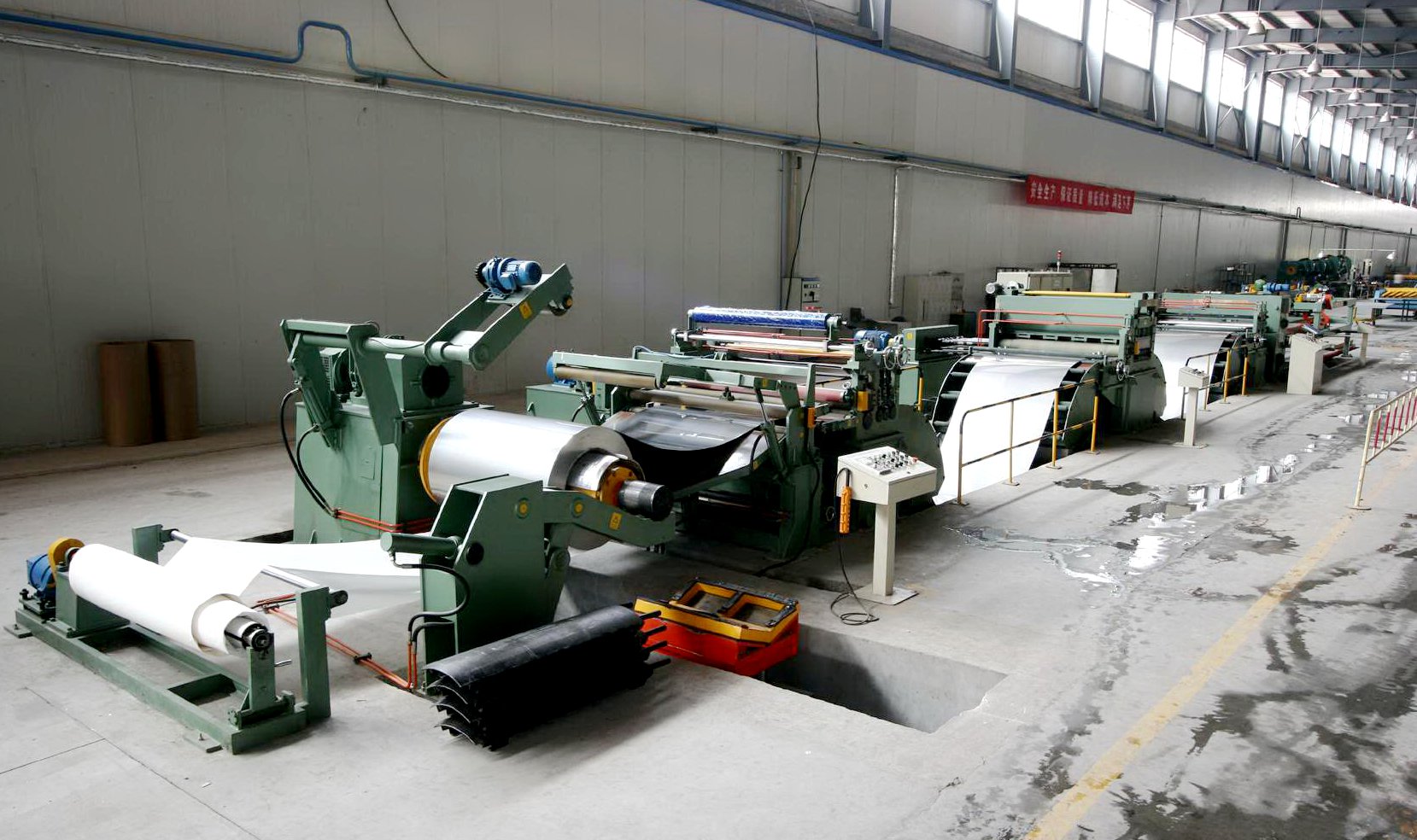
718 nickel-based alloy is a high-strength, high-temperature, and corrosion-resistant material, commonly used in aerospace, energy, and chemical industries. The general mechanical properties of 718 nickel-based alloy include:
Tensile Strength: The tensile strength of 718 nickel-based alloy typically ranges between 965 to 1035 megapascals (MPa), exhibiting high strength.
Yield Strength: The yield strength of 718 nickel-based alloy typically ranges between 690 to 930 MPa, indicating the stress level at which plastic deformation begins during loading.
Elongation: The elongation rate of 718 nickel-based alloy generally ranges between 12% to 30%. Elongation indicates the degree of plastic deformation a material can withstand before fracture, representing its ductility.
Hardness: The hardness of 718 nickel-based alloy typically ranges between 30 to 35 Rockwell Hardness (HRC). Hardness measures the material’s resistance to localized plastic deformation and scratching.
Additionally, 718 nickel-based alloy has good corrosion resistance, capable of resisting erosion by acidic, alkaline, and chloride media. It maintains high strength and stability at high temperatures, making it widely used in components and parts for high-temperature and corrosive environments.
Application Areas of 718 Nickel-Based Alloy
Aerospace: 718 nickel-based alloy, with its excellent high-temperature stability and oxidation resistance, is commonly used in manufacturing components for jet engines and rocket engines, including blades, disks, valves, and retaining rings.
Nuclear Industry: In the nuclear industry, 718 nickel-based alloy is often used to manufacture reactor structures and components, such as core support structures and fuel rods.
Oil and Natural Gas Industry: In the oil and natural gas industry, 718 nickel-based alloy, due to its good corrosion resistance and high-temperature resistance, is commonly used in manufacturing downhole equipment, pipelines, valves, and pumps.
Chemical Industry: In the chemical industry, 718 nickel-based alloy is used to manufacture various chemical reactors, towers, and storage tanks, maintaining stability in various chemical environments.
Advantages of 718 Nickel-Based Alloy
The advantages of 718 nickel-based alloy are mainly reflected in the following aspects:
Excellent Mechanical Properties: 718 nickel-based alloy has high tensile strength, yield strength, and hardness, along with good plasticity and toughness, suitable for manufacturing equipment that needs to withstand high pressure and high temperatures.
Superior Corrosion Resistance: With high amounts of nickel and chromium, 718 nickel-based alloy has excellent corrosion resistance, remaining stable even in acidic, alkaline, and saline environments.
Good High-Temperature Stability: 718 nickel-based alloy has good high-temperature stability, maintaining good mechanical properties and oxidation resistance even in high-temperature environments.
Wide Range of Applications: Due to these advantages, 718 nickel-based alloy is widely used in aerospace, nuclear industry, oil and natural gas industry, chemical industry, and other fields.
In summary, the outstanding performance and wide application areas of 718 nickel-based alloy make it a preferred material in many industrial fields. Its unique elemental content and chemical composition provide excellent corrosion resistance, high-temperature stability, and superior mechanical properties. This allows 718 nickel-based alloy to exhibit stable performance in various extreme environments, meeting the needs of high pressure and high temperatures. With the advancement of technology and the development of new materials, we can expect the applications and advantages of 718 nickel-based alloy to further develop and enhance.
Although 718 nickel-based alloy has many advantages, it also faces some challenges, such as the potential for cracking during welding and intergranular corrosion in certain environments. Therefore, research and development of 718 nickel-based alloy continue to overcome these challenges, further improve its performance, and expand its application areas.
In conclusion, 718 nickel-based alloy is a highly important alloy material with a broad application prospect. Its excellent performance and wide application areas make it play a significant role in many industries. With the progress of technology and the development of new materials, we look forward to greater breakthroughs in the applications and performance of 718 nickel-based alloy in the future.
At Aoxing Mill, we specialize in the production of 718 nickel-based alloy, a material renowned for its exceptional properties in extreme conditions. Our commitment to quality and innovation ensures our alloy meets the highest standards, supporting industries from aerospace to chemical processing.
Post time:
Jan-02-2024